Industrial parts washing systems are crucial to maintaining efficient production, but maintenance lapses can lead to costly downtime, reduced cleaning quality, and safety hazards. In this blog, we explore practical strategies to prevent maintenance issues on your industrial parts washing system and keep it running at peak performance.
1. Monitor Cleaning Performance of Industrial Parts Washing Systems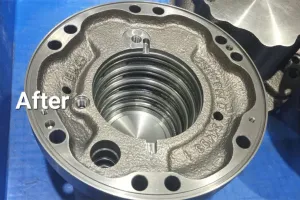
- Decline in cleaning quality: A persistent drop in wash effectiveness often signals issues like clogged nozzles, worn pumps, or degraded chemical solutions.
- Solution: Implement routine inspections of spray nozzles and filters, test the concentration of the cleaning solution, and replace components proactively.
2. Watch Efficiency and Operation Metrics
- Rising cycle time or energy/water use: These inefficiencies may indicate that the performance of the heating element, pump, or filtration system is slipping.
- Solution: Track performance metrics (cycle time, energy usage, chemical consumption) daily or weekly to catch anomalies early.
3. Listen for Warning Signs in Industrial Parts Washing Equipment
- Noise alerts: Unusual vibration or squealing can come from misaligned belts, failing bearings, or loose parts
- Error codes: Don’t ignore diagnostic system alerts. They often preempt major failures.
- Solution: Train staff to log and respond to changes in noise levels. Build familiarity with error codes and incorporate code checks into regular inspections to ensure optimal performance.
4. Check for Leaks in Industrial Parts Washing Systems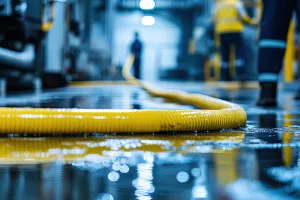
- Fluid leaks: Leaky hoses, seals, or connectors reduce system efficiency and can create slip hazards, as well as increase chemical usage.
- Solution: Include quick visual and tactile leak checks in daily rounds. Replace worn seals and tighten connections immediately.
5. Adopt Preventive and Predictive Maintenance
- Preventive maintenance: Activities like cleaning, lubrication, and scheduled filter replacement help avoid breakdowns
- Predictive maintenance: Using condition-monitoring tools (e.g., vibration, oil analysis) can spot issues before they escalate
- Solution: Develop service intervals (daily, monthly, or annually) and consider investing in smart sensors for vibration, fluid condition, and pump current monitoring.
6. Schedule Inspections for Industrial Parts Washing Machines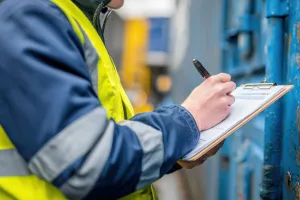
- Monthly: Grease moving parts, check seals and filters(Daily), replace filters weekly or sooner if needed, inspect heating elements for scale buildup and leaks
- Quarterly: Clean entire system, replace filters, inspect hoses, belts, and mechanical parts
- Annually: Perform full-system audit, including bearing cleaning, lubrication overhaul, control system testing, and alignment checks.
7. Train Operators and Maintenance Personnel
- Skilled teams are essential: Training should include machine operations, safety SOPs, routine maintenance, troubleshooting, and understanding diagnostic systems
8. Ensure Safety and Compliance in Parts Washing System Maintenance
- Electrical, chemical, mechanical safety: Regularly inspect wiring, grounding, seals, and ventilation systems to prevent fire, shock, or exposure risk
- Solution: Integrate safety checks into standard maintenance, ensure lockout/tagout protocols, maintain a clean workspace, and up-to-date PPE.
Benefits of Robust Maintenance on Your Industrial Parts Washing Systems
Benefit | Description |
Reduced Downtime | Fewer unexpected failures translate to higher availability and throughput |
Lower Operating Cost | Preventive steps and predictive maintenance reduce repairs, energy consumption, and chemical usage. |
Extended System Life | Regular care extends component life and delays capital replacement. |
Cost Control | Scheduled maintenance enables efficient resource planning and avoids emergency repair costs |
Well-maintained industrial parts washing systems deliver consistent cleaning, safety, and cost-efficiency. To prevent maintenance pitfalls:
- Set a clear inspection schedule: daily, monthly, and annually.
- Monitor performance closely (cycle time, energy, output quality).
- Listen to your system: noises and alerts signal early problems.
- Train your team intensively in operations and diagnostics.
- Apply preventive maintenance and introduce predictive tools.
- Integrate safety into every maintenance step.
By adopting this proactive maintenance framework for your industrial parts washing systems, you’ll preserve uptime, enhance cleaning outcomes, and control operational costs, bolstering ZERUST®/EXCOR®‘s reputation as an industry leader in protection and cleanliness solutions.