In today’s manufacturing environment, sustainability is more than a trend; it’s a necessity. As a result, forward-thinking operations are increasingly prioritizing environmentally responsible practices that reduce energy consumption, minimize waste, and extend the lifecycle of industrial components. One area that holds significant potential for sustainability improvements is parts cleaning.
At ZERUST®, we recognize the importance of optimizing your operations not only for efficiency but also for environmental stewardship. This blog explores best practices and innovative solutions for implementing sustainable parts cleaning processes in industrial and manufacturing settings.
Why Sustainable Parts Cleaning Matters
Traditional parts cleaning methods often involve high volumes of water, hazardous chemicals, and energy-intensive equipment. These approaches can contribute to environmental degradation, regulatory challenges, and increased operational costs. In contrast, sustainable solutions are designed to:
- Reduce chemical and solvent use
- Minimize water and energy consumption
- Improve worker safety
- Lower total cost of ownership
- Comply with environmental regulations
1. Use Water-Based Agents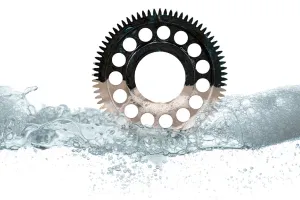
Conventional solvents can be harmful to both the environment and human health. Instead, opt for water-based solutions that offer high-performance degreasing and contamination removal, free from hazardous VOC emissions. ZERUST® offers a line of environmentally friendly water-based cleaners that combine efficacy with responsible chemical profiles.
2. Optimize Equipment Efficiency
Upgrading to energy-efficient parts cleaner equipment, such as spray washers with programmable cycles and energy-saving heaters, can significantly reduce power consumption. Closed-loop systems with filtration features also reduce the need for frequent fluid changes, extending the life of your cleaning solutions and lowering waste output.
3. Implement Precision Cleaning Techniques
Instead of relying on large-scale immersion or spray operations, consider targeted cleaning methods, such as ultrasonic. This technique enables the more precise application of cleaning energy and chemicals, thereby reducing overall resource usage and enhancing cleaning results.
4. Extend Cleaning Bath Life with Fluid Management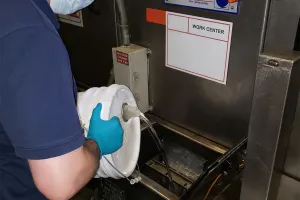
Regular monitoring and maintenance of cleaning fluids help ensure that your parts cleaner remains effective over time. Using inline filters, oil separators, and titration testing allows for more accurate management of bath chemistry. Unlike conductivity or Brix readings, which are better suited for rinses, titration offers a more reliable method for monitoring the concentration of cleaners and rust preventatives. These practices reduce sludge buildup, extend fluid life, and minimize waste.
5. Recycle and Reuse Cleaning Media
Where feasible, implement systems that enable the recycling and reusing of cleaning fluids. Technologies such as membrane filtration, distillation, and centrifugation can regenerate media, reducing waste disposal requirements and procurement costs.
6. Integrate Corrosion Protection into Cleaning
Combining parts cleaning with corrosion protection minimizes the need for multiple post-cleaning processes. Streamline operations by using ZERUST® Axxatec™ DA products, which provide dual-action cleaning and rust prevention. These water-based, low-foaming solutions effectively remove light hydrocarbon soils, leaving a dry-to-touch, clear protective film on metal surfaces. Ideal for spray, dip, or in-line applications, Axxatec™ DA helps reduce chemical use and processing steps while protecting parts during assembly, storage, or shipment.
7. Train Staff in Eco-Friendly Procedures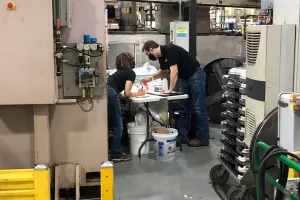
A sustainable process is only as effective as its execution. Ensure that your team is trained in proper dosing, machine operation, and environmental best practices to minimize the overuse of chemicals and energy while maintaining effective cleaning.
8. Monitor and Measure Environmental Impact
Utilize data logging and performance tracking tools to monitor energy use, chemical consumption, and waste output. As a result, these insights enable continuous improvement and help meet corporate sustainability goals.
9. Choose Suppliers with Green Initiatives
When selecting equipment and chemicals, partner with vendors who are committed to sustainability and actively develop solutions that align with green manufacturing principles.
10. Design for Cleanability
Engineering components for ease of cleaning, such as reducing blind holes, recesses, and complex geometries, can improve results with less effort and resource input. Cleanable designs reduce the need for aggressive chemicals or extended wash cycles.
ZERUST®: Your Partner in Sustainable Parts Cleaning
At ZERUST®, we deliver more than just corrosion protection; we provide integrated, sustainable solutions for your parts cleaning operations. Our corrosion-inhibiting cleaning products and VCI solutions are designed to minimize environmental impact while improving operational efficiency and extending part longevity.
Whether you are retrofitting your existing system or designing a new line, ZERUST®/EXCOR® can help you implement best practices that align with your environmental and performance goals.
Contact us today to learn more about our sustainable solutions and how we can help you transform your maintenance and corrosion protection processes.